Heat loss from basements accounts for a significant portion of the energy loss from a home. In many jurisdictions, basement insulation is a building code requirement. Cost usually determines the type of insulation system used. Unfortunately, safely insulating basement walls requires consideration of many factors in addition to reducing thermal conductivity across the foundation wall. Moisture dynamics must be considered in detail before insulating a basement wall. Materials used to insulate a basement wall must be selected based on their ability to control the flow of moisture and air as well as heat. Selecting the wrong type of insulation or placing it in the wrong wall assembly often leads to moisture accumulation with subsequent material deterioration and growth of mold.
The Problem
Meeting Energy Star levels of performance is one of the criteria for constructing homes to Building America levels of performance – levels defined by the Building Science Consortium and others. Homes constructed with basements require some degree of basement insulation to meet Energy Star. As a result all Building America homes with basements constructed by the Building Science Consortium have basement insulation.
In any event, heat loss from basements accounts for such a significant portion of the energy loss from a home that it is clear that a home with a basement must have basement insulation to be called "energy efficient." Additionally, in many jurisdictions, basement insulation is a building code requirement.
Finally, most homeowners with homes with basements finish the basement area for additional living space. When they do, they typically insulate the perimeter walls. Homes with basements often end up with basement walls that are finished and insulated.
There are only three ways to insulate a basement wall: on the interior, on the exterior or in the middle (Figure 1). Of the three, the most common approach has been to insulate basements internally. The reasons for this have been due almost strictly to cost.
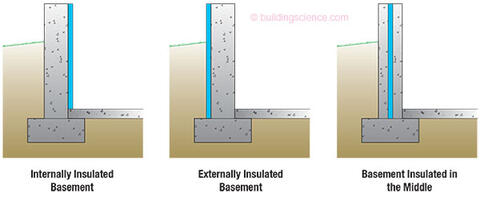
Figure 1: Basement insulation locations
Externally insulated basements have a major cost factor associated with protecting the exposed above grade portion of the insulation assembly and shifting the house structure outward to compensate for the thickness of the exterior basement insulation (Figure 2). Most protection systems involve some form of rendering (stucco, synthetic stucco, cement parge coats, etc) that have proven to be not durable (the “weed-whacker” problem). Furthermore, protecting the exposed insulation system during the construction process until it gets covered has also been a major challenge—so muchh so that most builders who have done it once, do not want to do it again.
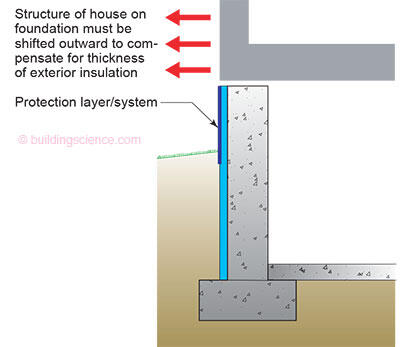
Figure 2: Costs associated with exterior basement insulation: protection layer/system for exposed insulation above grade wall; change in practice requiring exterior shift of house structure; protecting exposed insulation during construction process until protection layer/system can be installed
Internally insulated basements are often coupled with interior basement finishing and therefore offer a “higher perceived value” to the homebuyer. “My basement is almost finished – I just have to add drywall…”
For these reasons most basements are insulated internally.
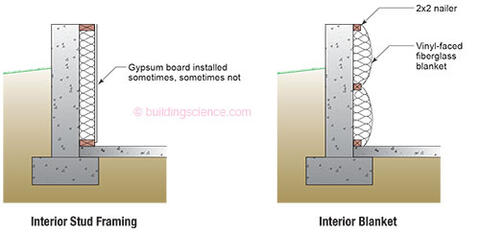
Figure 3: Interior insulation approaches
All Building America homes constructed by the Building Science Consortium were initially constructed with interior basement insulation. The approaches used early in the program were interior stud wall framing insulated with fiberglass batts and “blanket” insulation (Figure 3). These two approaches are the most common approaches to basement insulation used by the home building industry in general. Photographs 1, 2, 3 and 4 illustrate the two approaches. Note the installation of an interior vapor barrier in Photograph 2, and the impermeable interior surfaces in Photograph 3 and Photograph 4.
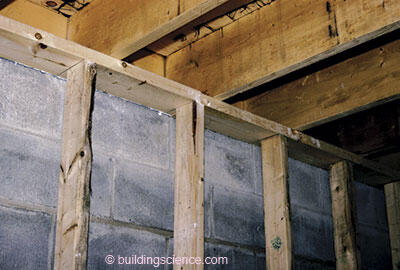
Photograph 1: Interior stud framing located at basement perimeter
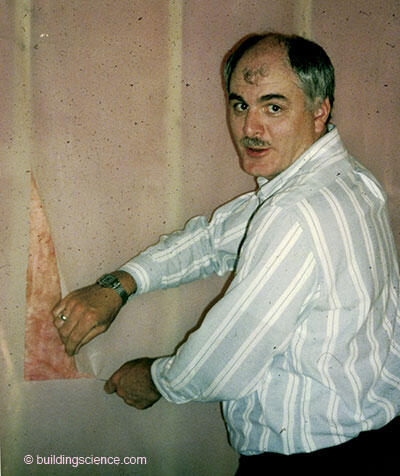
Photograph 2: Interior basement stud framing insulated with fiberglass batts covered with a polyethylene vapor barrier
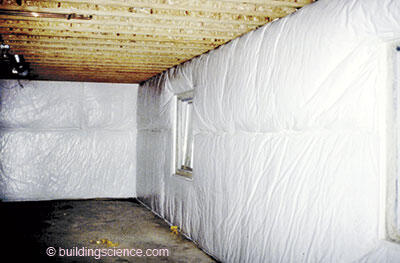
Photograph 3: Blanket insulation with impermeable vinyl interior surface
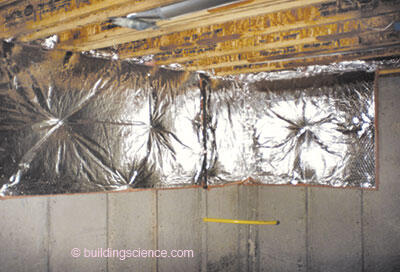
Photograph 4: Blanket insulation with impermeable aluminum foil interior surface
The experience by the Building Science Consortium with these two approaches has been bad. The Building Science Consortium has concluded that these two approaches are unsuitable for use by the home building industry due to serious problems associated with mold, decay and odors. This is consistent with reports from Canada where basements are insulated in a similar manner (Fugler, 2002) and from other researchers in the United States, notably in Minnesota (Ellringer, 2002). Continued use of these approaches by the home building industry will likely lead to a disaster of unprecedented proportions and may result in the construction of energy efficient homes being set back a generation.
The Physics of the Problem
The problem associated with interior stud wall framing insulated with fiberglass batts and “blanket” insulation is due to the accumulation of moisture within the insulated frame wall located on the interior of the basement foundation or within the blanket insulation located on the interior of the basement foundation wall. This moisture leads to mold, decay and odors.
Moisture enters the insulated assemblies due to five wetting mechanisms:
- Moisture of Construction (Figure 4)
- Air Leakage (Figure 5)
- Capillary Rise (Figure 6)
- Diffusion (Figure 7)
- Ground Water Leakage (Figure 8)
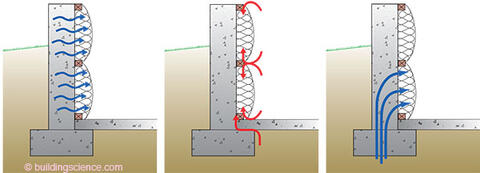
Figure 4 (above left): Moisture of construction—Thousands of pounds of water are contained in freshly placed concrete in basement foundation walls; drying in uninsulated exposed walls takes many months, longer in walls with impermeable insulation systems
Figure 5 (above middle): Air leakage from interior and from exterior under slab—This is the "summer" problem where interior moisture laden air leaks into insulation systems and contact cold concrete or masonry; can also be a winter problem, but is not usually common due to typically lower winter interior relative humidities-except in severe cold climates (greater than 8.000 heating degree days)
Figure 6 (above right): Capillary rise through footing—This was rarely a problem until foundation walls became insulated on the interior with impermeable layers
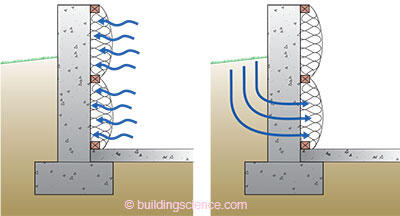
Figure 7 (above left): Diffusion from interior—This is also a “summer” problem; occasionally a “winter” problem
Figure 8 (above right): Groundwater leakage through foundation—Major problem with water sensitive interior insulation and finishing systems
The internally insulated frame wall and blanket insulation approaches are unable to adequately handle these wetting mechanisms singularly or in combination. These two approaches are constructed with vapor barriers or with vapor retarders and are incapable of allowing foundation walls to dry to the interior. This is an issue with moisture of construction, capillary rise and ground water leakage. Simply leaving off interior vapor barriers and vapor retarders will not work due to the issues associated with interior vapor diffusion.
Additionally, these two methods are incapable of being constructed in an airtight manner using typical production trades and materials and therefore are unable to address the air leakage wetting mechanism.
Finally, these two methods are constructed with moisture sensitive materials and therefore are unable to tolerate even minor groundwater leakage, therefore requiring builders to be “perfect” in controlling groundwater – an impossible requirement.
The problems with these two common approaches to interior basement insulation manifest themselves in mold, decay and odors (Photographs 5, 6 and 7).
The problems experienced by the Building Science Consortium with Building America homes constructed with internally insulated basements and the reported similar problems by others in the building industry led to a major effort to develop insulation approaches to basement construction that did not result in mold, decay and odors. The effort was not limited to the construction of new homes, but also focused on the insulation retrofit of existing basements. The nature of the problem for existing homes was deemed to be similar to the problem associated with the construction of new homes.
The experience acquired by the Building Science Consortium has been reflected in changes that have been made to the Builder’s Guide Cold Climate (Lstiburek, 2001) as well as those for Builder’s Guide Hot-Dry & Mixed-Dry Climate (Lstiburek, 2000) and Builder’s Guide Mixed-Humid Climate (Lstiburek, 2001). All recommended basement interior insulation strategies involve placement of a layer of rigid foam insulation against the foundation wall. The moisture sensitive interior wood framing and paper faced gypsum board are no longer in contact with the major moisture source – the concrete or masonry foundation wall. . .
Download complete report here.